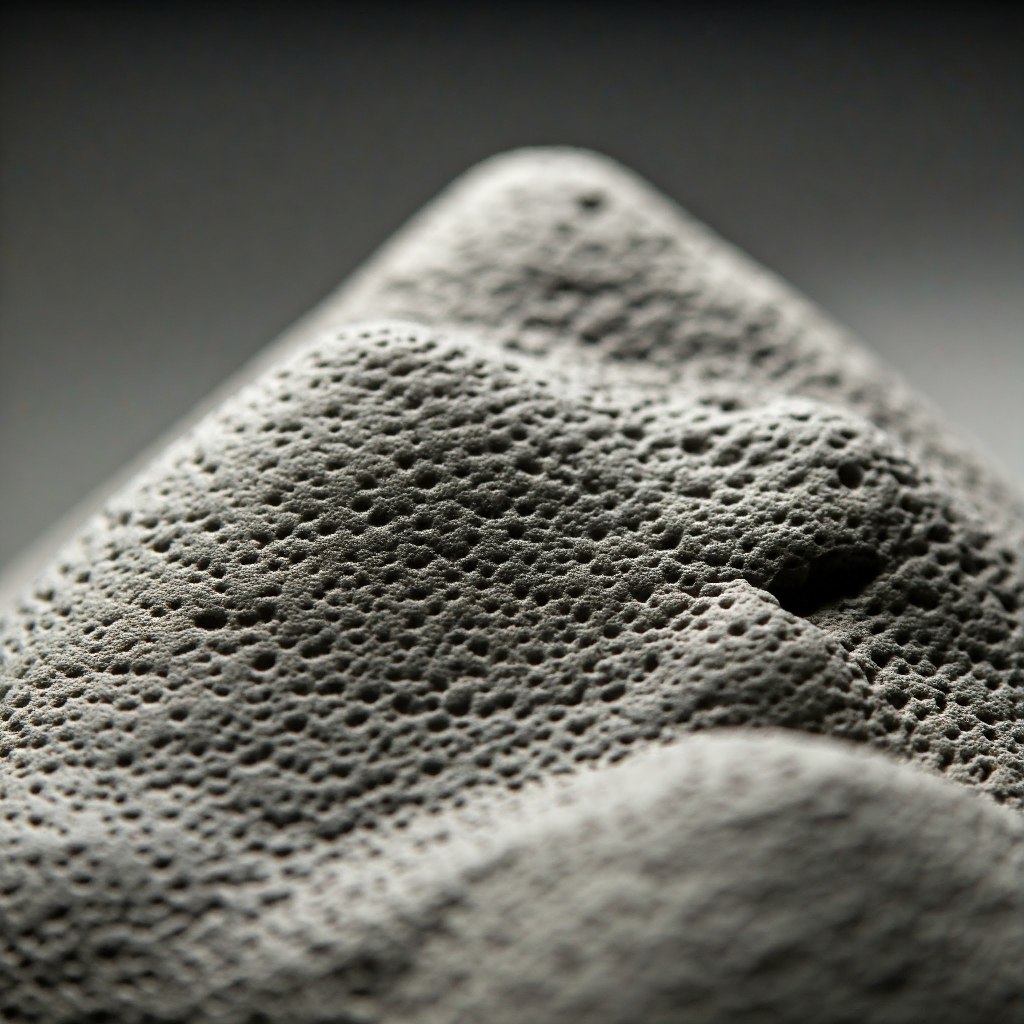
Geopolymer Technology
Geopolymer (GP) is alumina silicate polymeric network forming an inorganic binder that can perform similar or ever superior to Portland cement.
In India, Construction and Infrastructure industry exerts a lot of environmental pressure by consuming natural assets and cement produced by energy intensive production process. Cement production is responsible for around 10% of global CO2 emissions. India faces dual challenge of reconciling its rapid economic growth with a pressing need to address climate change.
Statistics reveal that 1 tonne of Geopolymer emits – 0.16 tonne of CO2, whereas 1 tonne of Portland cement emits -0.87 tonne of CO2.
Geopolymer Concrete (GPC) is similar to conventional Portland cement concrete wherein Conventional Portland Cement paste is replaced by Geopolymer paste and the aggregate system basically remains same. The Geopolymer paste is made from GSMs and the Geopolymer Reaction Generation Liquid (RGL)
GSMs (Geopolymeric Source Material) are materials containing alumina and silica such as Fly ash, Ground Granulated Blast Furmace Slag- GGBS with RGL Solution.
There are Numerous Examples of Field Applications of GPC Technology:
- World’s first Structural Building in the University of Queensland’s Global Change Institute (GCI) Australia.
- Structures in Ukraine
- Heavy duty pavements in Brisbane West Well Camp Airport (BWWA), VicRoads in Australia.
In India: GPCs have been successfully tried for the production of building elements such as Fly Ash Bricks, Blocks, Ventilators, Hexagonal Paver, Zigzag Paver, Fencing Pole, Kerb Stone, Compound wall cladding, Interlocking Columns, Sanitary Rings, Kilometer Stone, Name Board, Forest Guard Stone, Tree Guard etc.,
The first National Geopolymer Technology Demo Centre was inaugurated on 30th January 2019 at CASHUTEC (Centre for Ash Utilization Technology & Environmental Conservation) at CUSHUTEC NK, Raichur by District Collector, Raichur with the support of CACR, SRMIST (formerly SRM University), Chennai as Knowledge Partner and Kuttuva Silicates Private Limited (KSPL), Madurai as Industry Partner.
Properties of Reaction Generating Liquid (RGL)
- The density is the range of 1.20+/-0.05 kg / lit.
- The Molar weight Ration of SiO2/Na2O in the RGL is about 0.55 to 0.60
- Viscosity of the liquid is in the range of 25-50 Centipoise.
- The storage life in air tight container is generally 45-60 days(when stored inside the building without direct exposure to heat, sunlight and rain, etc.,)
- General Precautionary and safety measures are as applicable to handing of sodium hydroxide and sodium silicate solutions must be adopted.
- Any addition of water to RGL without prior tests is not permitted.
Recent Successful Projects done by CACR-SRMIST & KSPL in India.
- Road construction Project of 0.5 Kilometer laid at M/s.RKM Powergen P. Ltd., – A Thermal Power Generation Company in Raigarh District in Chhattisgarh State. In the Road Construction project, no water should be added. Only RGL alone is to be added in the admixture of road construction material such as sand, Coarse materials and other ingredients. Normal Cement Road Project requires minimum 2-3 weeks curing time whereas GPC Projects require air setting time of 48-72 hours only.
- Successfully developed Paver Blocks with M40 grade in MSME paver blocks manufacturer.
- CASHUTEC has successfully produced precast components and the company can setup toilet of 4 feet X 4 feet within 45 minutes under Swach Bharath Scheme with GPC Technology.
- Many more Projects like Road Construction Project and Paver blocks production with GPC Technology are going to be taken by CACR-SRMIST with the support of KSPL at JSW Steel Plants at Merchery, Salem., etc.,